When BI isn’t Enough: The Essential Role of AI in Connected Vehicle Analytics
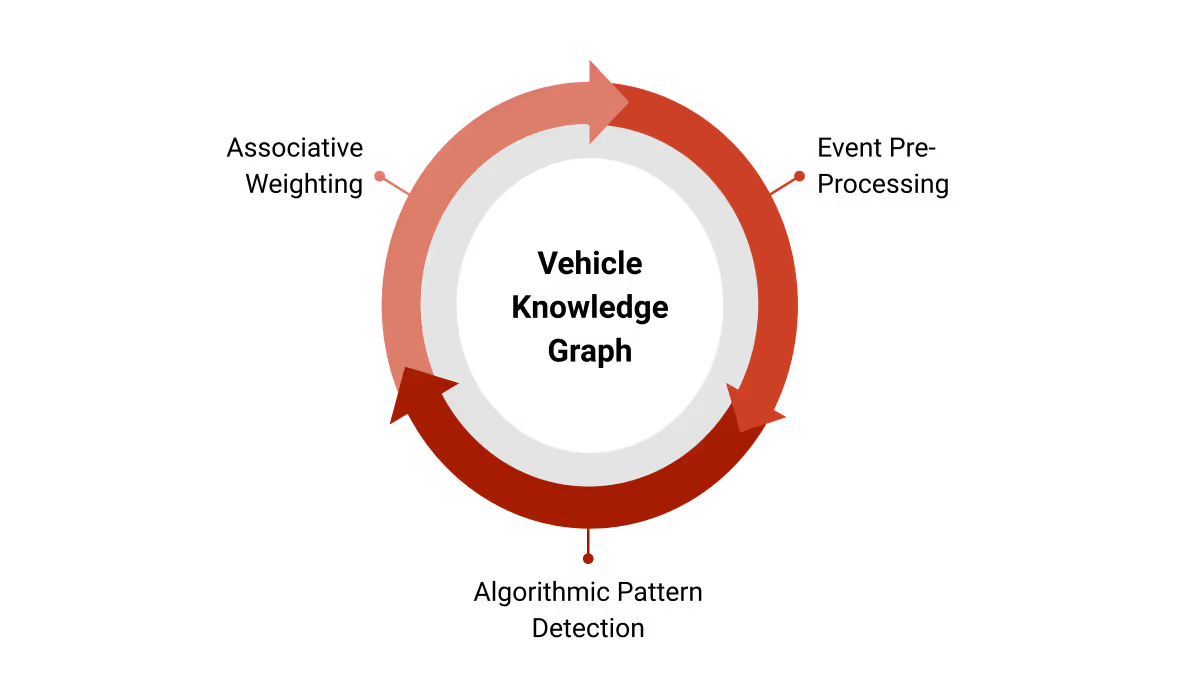
The Promise of Connected Vehicle Data
The automotive industry is undergoing a data revolution. As vehicles become increasingly connected, they generate a torrent of data that harbors the potential to dramatically enhance quality and service operations of vehicle manufacturers (OEMs). From earlier detection of production issues to predictions of individual vehicle and component failures to reduced service times, the potential for lower expenses, higher revenues and improved customer experience is enormous.
However, the sheer volume, complexity, heterogeneity, and the time-series nature of connected vehicle data present significant challenges to realizing this vision. While powerful Business Intelligence (BI) tools are necessary for doing so, they alone are not sufficient. The key to unlocking value lies in deploying a more sophisticated tool, high-dimensional time-series Artificial Intelligence (AI).
In this post, we'll explain what BI is, how it is typically used in quality processes, and why it is insufficient for leveraging connected vehicle data. We will then contrast the BI status quo with a modern system that leverages an AI-infused knowledge graph (Viaduct TSI Engine) and workflow to transform the quality process.
Limitations of BI
What does BI do?
For the purpose of this discussion, we’ll talk about BI less as a singular technology or product than as an approach to data analysis that relies on the following capabilities:
- The ability to connect disparate data sources into a unified data model - BI tools either provide or can work with related data integration technologies that combine typical connected vehicle data sources across manufacturing, telematics, diagnostics, and service data.
- The ability to query and visualize disparate data sources - BI tools excel at providing a rich and customizable visualization and point-and-click analysis portals for a range of typical relational data sources. Some specialized BI tools and plug-ins can also provide rich presentation of time-series data.
- Handling of big data at scale - Modern BI architectures have evolved to the point where they can now handle large batches of data, including handling the kinds of volumes of data we see transmitted from large fleets of vehicles. While querying “big data” still comes with its challenges, with the right technology and skills it is a solvable problem.
Why BI falls short
While BI tools are required for any data analysis process, they are far from sufficient to deliver business impact on connected vehicle data. BI tools operate under a reactive model, i.e., they only respond to queries presented to them by users. BI tools fail to offer users the guidance they need to navigate the scale and complexity of connected vehicle data. This limitation creates major challenges that are difficult or impossible for users to overcome:
- Too much trial and error - Connected vehicle data has extremely high dimensionality (1000s of vehicle attributes, 1000s of fault types, 1000s of failure types) and is temporal in nature (i.e., many signals come in time-sequenced streams). Traditional trend and pareto analysis supported by BI platforms, while useful, is highly inefficient. It is too cumbersome and in some cases impossible to manually “slice-and-dice” your way to the root cause of a trending type of warranty claim or fault code across data with this level of complexity.
- Questions asked the wrong way - With a good BI tool, it is possible to see which fault code is happening most often in a particular type of vehicle. This is what most analysts will reasonably do with a typical BI tool, but the answer to this question isn’t really what’s needed. To separate signal from noise, a good query should normalize total counts of fault codes by the number of vehicles on the road, compare against typical occurrence rates from the past and compare rates across segments of the vehicle population. While a skilled quality engineer might know these are the right questions to ask, and a skilled data engineer might be able to write these queries manually, most BI tools will not provide this kind of power or flexibility without weeks of custom development.
- Response times are slow - This type of custom development and ad hoc data crunching is slow from both an operational and a technical perspective. First, there is the handoff between the quality engineer and the data engineer. Then there is the problem that in the presence of hundreds of millions or billions of signals across millions of vehicles, manual queries and visualizations are slow to run and expensive to maintain.
The Power of AI
What does AI do?
While BI tools are crucial building blocks for vehicle data analysis, without AI that is tightly integrated into business processes, this analysis will be slow and ineffective. AI systems, such as Viaduct’s patented Temporal Structural Inference (TSI) Engine, can change this. While AI is a broad category with a myriad of technologies, it is not merely an industry buzzword. Rather, we define AI as a tool that serves users by preemptively surfacing relevant information, enabling them to navigate complex environments with enhanced clarity and foresight. If BI is like a flashlight that can be used to interrogate data to uncover insights, AI serves the crucial role of telling a person where to shine their flashlight. It guides them to the right questions based on the context of the process they are executing and then provides answers that are relevant to the next action that should be taken.
How AI Creates Transformative Value
Among the OEM processes being transformed by AI is quality, especially in post-production settings. Field quality refers to the process whereby teams of investigators monitor data coming from fleets of in-service vehicles, looking for patterns and evidence of systemic quality issues. Traditionally these investigators have relied heavily on manual review and analysis of warranty claims and service records to flag potential issues.
With the advent of connected vehicles, it is now possible to monitor fault and sensor data, giving investigators orders of magnitude more data to parse through. While BI platforms, even those designed to handle big data, might technically provide the flashlight required to see important patterns, without AI there is just no way a human investigator can efficiently explore the vast amount of data at their disposal. An AI solution tailored to the needs of finding systematic quality issues is a must-have.
Let’s see how the AI-based TSI Engine works in the field quality context as an example.
Building a knowledge graph
As an AI-based system, the TSI engine must first be primed with data to build up a knowledge graph. The steps involved in priming the system include (see figure 1):
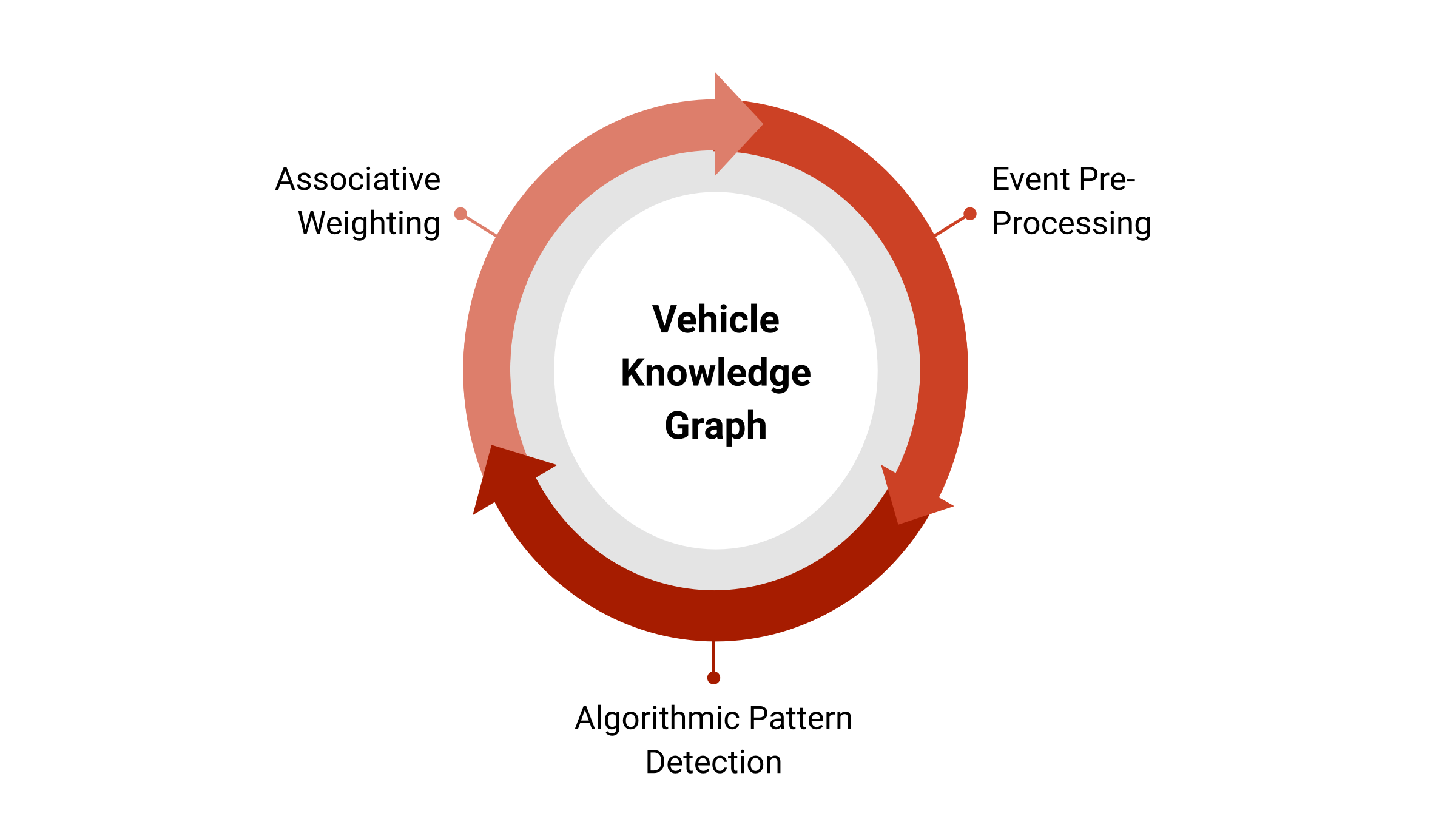
- Event pre-processing - turning raw sensor readings and claims data into interpretable events.
- Algorithmic pattern detection - various techniques can be employed to detect notable patterns of event occurrences. These patterns, whether common or rare, are grouped into nodes of the knowledge graph.
- Associative weighting - Nodes are related to each other, with each relationship scored to reflect the nature of the relationship and association strength. These scores comprise the edges of the knowledge graph.
The knowledge graph can be primed quickly and will deliver value, much like a BI platform can deliver value, just by making it possible for a human to access all their data in one place. But transformative value comes when users interact with the system as part of their process.
Leveraging Insights within a process
The quality process can be broken into four stages, each of which benefits in concrete ways from an AI-infused knowledge graph and workflow.
- Detect issue - AI is able to simultaneously evaluate Signal Events (aka DTC and or sensor events), Claim Events and Vehicle attributes to detect anomalies that can be scored on a matrix of associations it finds in the knowledge graph. The highest priority anomalies are served up to triage investigators as “suggested issues” that should be investigated.
- Investigate issue - Whether issues are surfaced by AI or by manual investigation, they should be captured in an integrated Issue Management System that can explicitly define an issue by the signal events, claim attributes, and vehicle attributes that are common to the issue. Quality analysts, problem solvers and product engineers can then collaboratively analyze and refine the Issue definition. AI helps by suggesting which related vehicle events (claim and DTC occurrences) and vehicle populations should be reviewed to determine what is and is not a cause of the issue.
- Resolve issue - Once an issue team is comfortable with an issue definition and has identified a fix to the problem, they can deploy field actions (TSBs, Voluntary Service Campaigns or Recalls). AI helps with this step by clarifying the conditions under which failure is most likely to occur. This information can be used to de-scope corrective actions or to stage service campaigns to fix high risk vehicles before low risk vehicles.
- Monitor issue - Even after an issue is resolved, the system continues to benefit from learning that happened during the course of the investigation. Not only can it monitor the effectiveness of the resolution, it can quickly detect new flare-ups of an old issue. Furthermore, the correlations between signal events, vehicle events, and vehicle attributes (part IDs, suppliers, plants, process, etc..) are used to strengthen inferences about future problems.
A Virtuous Feedback Loop
As an issue is investigated and refined the TSI engine takes input, learns from it, and starts a virtuous feedback loop with the investigative team. The TSI engine continues to suggest which correlations between telematics, service records, and vehicle attributes are most descriptive and predictive of the issue. User input helps the TSI engine narrow the boundaries of the search space so that it can run more sophisticated and computationally intensive algorithms that improve fidelity and accuracy of its suggestions.
As you can see in this example, AI is not an after-thought in the design of the field quality system. It is integral to every aspect of the workflow, and it turns a historically hunt-and-peck, wait-and-see exercise into a symbiotic barrage of proactive insights, questions and answers about an issue.
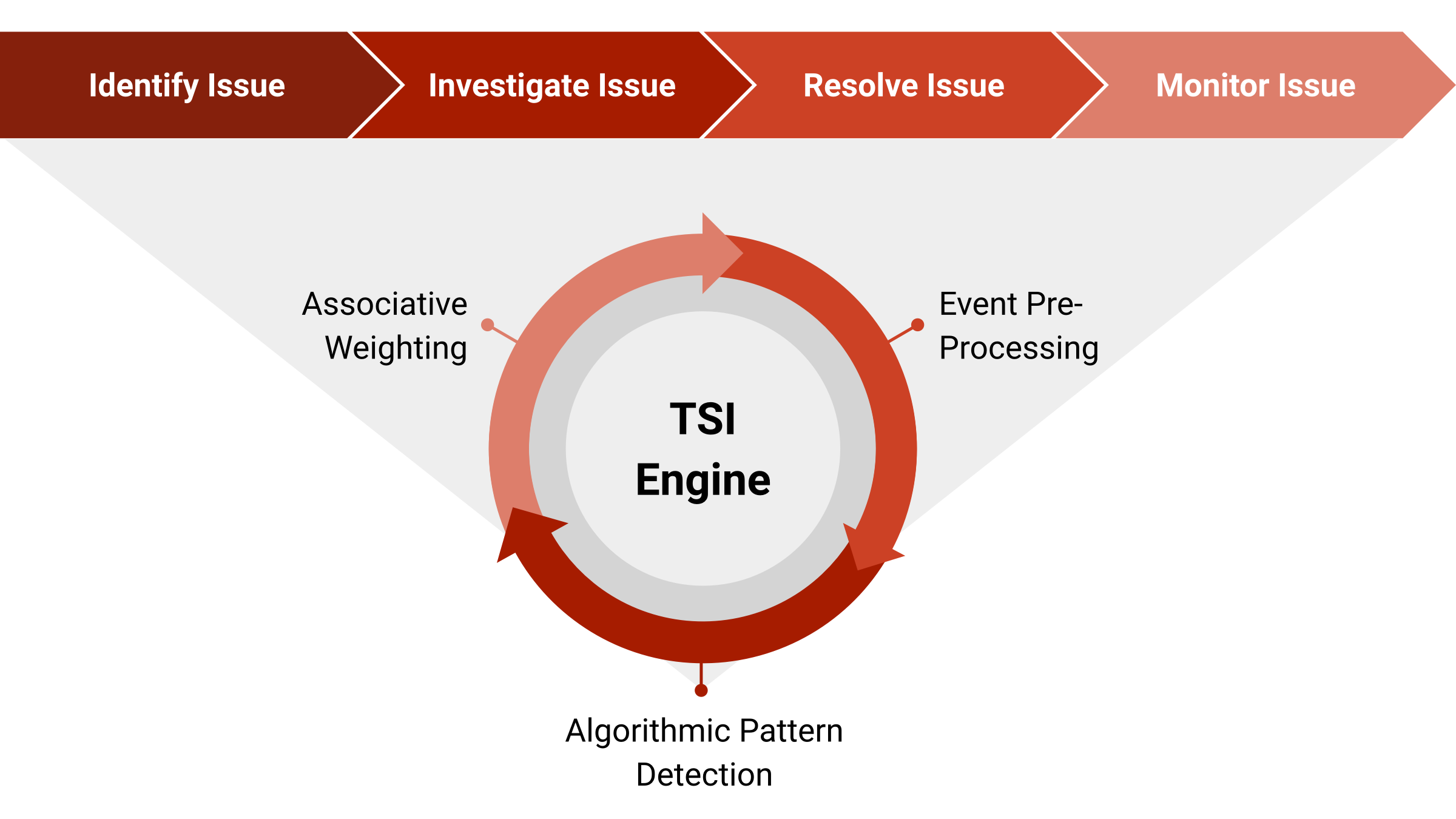
Conclusion: Business Transformation of the Future Requires AI
In summary, BI tools are adept at solving some of today’s quality challenges by helping OEMs integrate various data sources so vehicle and data experts don't have to work so hard to manually assemble, analyze, and present insights. However, future-proofing a quality process requires deploying purpose-built AI. By harnessing technology like Viaduct’s TSI Engine, OEMs can transform their organizations, converting their staff from data wranglers into problem solvers, finding issues faster, speeding up root cause analysis, and preventing vehicle failures before they occur!